Utrzymanie ruchu zakładów przemysłowych to zespół, często trudno mierzalnych czynników, których poprawne funkcjonowanie przyczynia się do sprawnego realizowania szeroko rozumianego procesu produkcji. Sprawne utrzymanie ruchu połączone z poprawnością wszystkich procesów biznesowych przyczynia się do wzrostu efektywności przedsiębiorstwa, a tym samym jego lepszej kondycji finansowej.
Służby utrzymania ruchu: Kluczowa rola w zakładach przemysłowych
Znaczenie utrzymania ruchu
Służby utrzymania ruchu odgrywają kluczową rolę w funkcjonowaniu zakładów przemysłowych. Dzięki nim maszyny i urządzenia pracują nieprzerwanie i bezawaryjnie. To z kolei pomaga uniknąć awarii, przestojów oraz kosztownych napraw i wymiany sprzętu. W rezultacie utrzymanie ruchu przyczynia się do zwiększenia efektywności firmy i poprawy jej sytuacji finansowej.
Utrzymanie ruchu stanowi nieodzowny element działalności zakładów przemysłowych, mający kluczowe znaczenie dla ich sprawnego funkcjonowania. Jest to kompleksowy zespół działań, który ma na celu zapewnienie optymalnego stanu maszyn, urządzeń oraz infrastruktury produkcyjnej. Poprawne funkcjonowanie utrzymania ruchu przyczynia się do efektywnego i niezakłóconego przebiegu procesu produkcji.
Rola służb utrzymania ruchu
Służby utrzymania ruchu mają za zadanie monitorować, konserwować i naprawiać maszyny oraz urządzenia w zakładach przemysłowych. Ich głównym celem jest zapewnienie ciągłej dostępności sprzętu, minimalizacja awarii oraz optymalizacja procesów produkcyjnych. Współpracują one zarówno z działami produkcyjnymi, jak i zespołami inżynieryjnymi, aby skutecznie zarządzać utrzymaniem ruchu w przedsiębiorstwie.
Kluczowe czynniki utrzymania ruchu
Skuteczne utrzymanie ruchu opiera się na szeregu czynników, które wzajemnie się uzupełniają. Oto kilka kluczowych elementów, które przyczyniają się do sukcesu służb utrzymania ruchu:
- Planowanie konserwacji i przeglądów regularnych: Służby utrzymania ruchu opracowują harmonogramy konserwacji i przeglądów, aby regularnie monitorować stan maszyn i urządzeń. Dzięki temu możliwe jest wykrycie i naprawa potencjalnych problemów przed ich eskalacją.
- Naprawa awaryjna: Służby utrzymania ruchu są gotowe do szybkiego działania w przypadku awarii maszyn. Ich zadaniem jest jak najszybsze przywrócenie sprzętu do działania, aby minimalizować przestój w produkcji.
- Optymalizacja procesów: Służby utrzymania ruchu analizują i optymalizują procesy produkcyjne, identyfikując obszary, w których można wprowadzić ulepszenia. Poprawa efektywności i wydajności maszyn przekłada się na lepsze wyniki przedsiębiorstwa.
- Szkolenia i rozwój personelu: Służby utrzymania ruchu inwestują w szkolenia i rozwój swojego personelu, aby zapewnić im niezbędną wiedzę i umiejętności techniczne do skutecznego zarządzania maszynami i urządzeniami.
- Zapobieganie awariom: Służby utrzymania ruchu podejmują działania prewencyjne, takie jak regularna konserwacja i kalibracja, aby minimalizować ryzyko awarii i przedłużać żywotność maszyn.
Korzyści wynikające z efektywnego utrzymania ruchu
Skuteczne utrzymanie ruchu przynosi wiele korzyści dla przedsiębiorstwa, w tym:
- Zwiększenie dostępności sprzętu i minimalizacja przestojów produkcyjnych.
- Zmniejszenie kosztów związanych z naprawami awaryjnymi i zastępczymi.
- Zwiększenie żywotności maszyn i urządzeń, co przekłada się na długoterminowe oszczędności.
- Zwiększenie efektywności i wydajności produkcji.
- Zminimalizowanie ryzyka wypadków i zagrożeń dla pracowników.
Podsumowanie
Służby utrzymania ruchu odgrywają kluczową rolę w zapewnieniu sprawnego i niezakłóconego funkcjonowania zakładów przemysłowych. Poprawne zarządzanie utrzymaniem ruchu przyczynia się do efektywności procesów produkcyjnych, co z kolei wpływa na kondycję finansową przedsiębiorstwa. Dlatego warto inwestować w rozwój i optymalizację służb utrzymania ruchu, aby zapewnić ciągłość produkcji i osiągnąć konkurencyjną przewagę na rynku.
Specyfika poszczególnych gałęzi przemysłu jest bardzo rozmaita. Nawet pozornie takie same fragmenty, mimo pewnych cech wspólnych różnią się między sobą szczegółami, rozwiązaniami technicznymi wynikającymi z procesów produkcyjnych. Już podejmowanie decyzji dotyczących zakupów agregatów / urządzeń linii produkcyjnych musi uwzględniać konkretne wymagania techniczne. A także uwzględniać uwarunkowania ekonomiczne i konkretne wartości użytkowe, jakie mogą być w ten sposób dodane do biznesu firmy lub stracone.
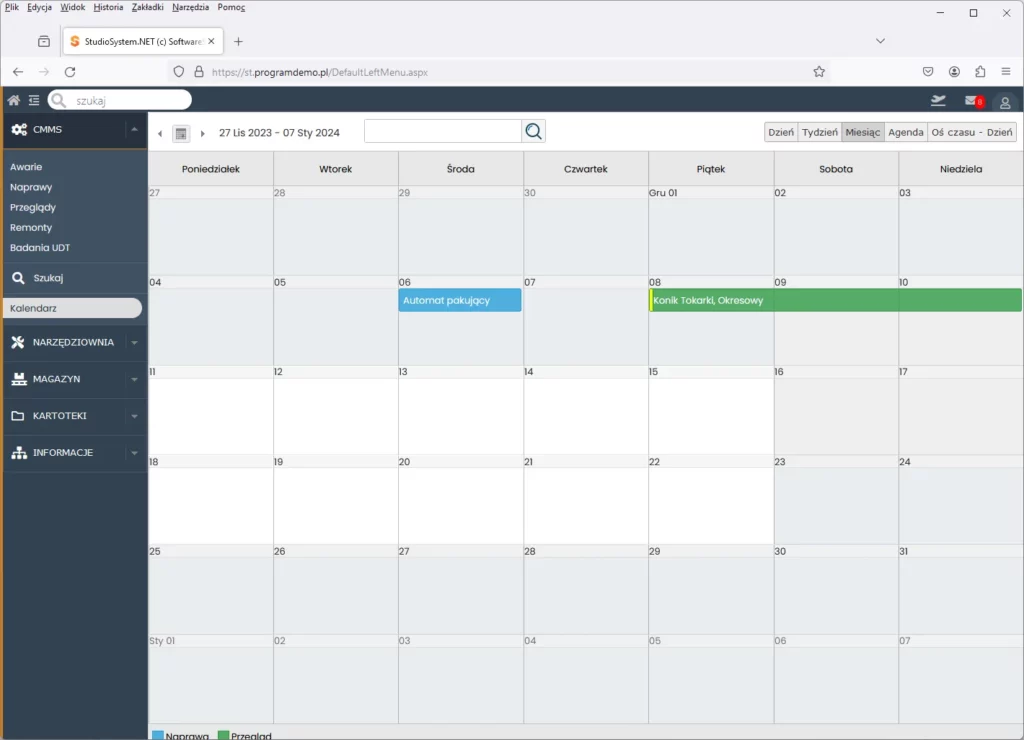
Sam zakup maszyn i urządzeń może być dokonywany w ramach inwestycji lub oparciu o siły własne. Każdorazowo decyzja powinna aspekt długoterminowych korzyści. Instalacja i wdrożenie urządzeń na etapie decyzji, przyjęcia stosownych metod i harmonogramu, samego procesu uruchamiania, musi być wielkiego zaangażowania służb utrzymania (UR). Owocem tych działań są wyniki testów i prób – zadowolenie naszego klienta – produkcji.
UR – utrzymanie ruchu to: komórka organizacyjna odpowiedzialna za efektywność gospodarki techniczo-organizacyjnymi zakładu.
W oparciu o uzgodnione modele działań i programy eksploatacji poszczególnych urządzeń realizowana jest polityka postępowania z urządzeniami, zasady stosowania konkretnych praktyk konserwacyjnych. W powiązaniu z istniejącą organizacją służb eksploatacyjnych UR wpływa to na powstawanie właściwych wzajemnych relacji: Techniki z Produkcją. Zazwyczaj proces ten przebiega bardzo wolno i z oporami, szczególnie wobec niechęci wyższego managementu zainteresowanego istnieniem status quo ze względu na brak wiary w skuteczność działań pracowników poziomu podstawowego. Zwłaszcza, gdy dodatkowym problemem okazują się pojawiające się wówczas kwestie komunikacji wewnętrznej.
Służby utrzymania ruchu – wprowadzenie
Służby utrzymania ruchu to działania podejmowane w celu zapewnienia ciągłej i niezawodnej pracy maszyn i urządzeń w zakładach przemysłowych. Ich zadaniem jest minimalizacja awarii, przestoju oraz kosztów związanych z naprawami i wymianą sprzętu. Utrzymanie ruchu jest kluczowe dla efektywnego funkcjonowania przedsiębiorstwa, a jego brak może prowadzić do poważnych strat finansowych.
Zadania służb utrzymania ruchu
1. Monitorowanie stanu technicznego maszyn i urządzeń
Pracownicy służb utrzymania ruchu regularnie sprawdzają stan techniczny maszyn i urządzeń, aby wykryć ewentualne usterki i zapobiec awariom. W tym celu stosowane są różne metody diagnostyczne, takie jak wibracyjna analiza maszyn, termowizja czy badania oleju.
2. Planowanie i przeprowadzanie przeglądów technicznych
Przeglądy techniczne są niezbędne do utrzymania maszyn i urządzeń w dobrym stanie technicznym. Służby utrzymania ruchu planują i przeprowadzają regularne przeglądy, w trakcie których dokonują niezbędnych napraw i wymian części.
3. Przeprowadzanie prac konserwacyjnych
Prace konserwacyjne mają na celu zapobieganie awariom i przedłużenie żywotności maszyn i urządzeń. Służby utrzymania ruchu przeprowadzają różnego rodzaju prace konserwacyjne, takie jak smarowanie, czyszczenie czy regulacja.
4. Naprawy i modernizacje
W przypadku awarii lub zużycia części, służby utrzymania ruchu przeprowadzają naprawy lub wymiany. Dodatkowo, w celu poprawy efektywności i wydajności maszyn, przeprowadzane są modernizacje i ulepszenia.
Znaczenie służb utrzymania ruchu dla przedsiębiorstwa
Sprawne utrzymanie ruchu maszyn i urządzeń jest kluczowe dla efektywnego funkcjonowania przedsiębiorstwa. Dzięki temu możliwe jest minimalizowanie kosztów związanych z awariami i przestoju, co przekłada się na lepszą kondycję finansową firmy. Dodatkowo, poprawność procesów biznesowych i ciągła praca maszyn i urządzeń wpływają na jakość produktów oraz zadowolenie klientów.
LIKWIDACJA URZĄDZENIA
Na etapie likwidacji urządzenia konieczne są metody działań UR uwzględniające efektywność decyzji: sprzedaż / złomowanie / utylizacja. Tym bardziej że przepisy unijne z tym związane nakładają szereg dodatkowych obowiązków, w których realizację są angażowane również właśnie służby UR.
TPM Total Productive Maintenance
Total Productive Maintenance (TPM) oznacza w dosłownym tłumaczeniu Totalne Utrzymanie Ruchu. W odróżnieniu od tradycyjnego podejścia do maszyn, w którym dział utrzymania ruchu, „gasząc pożary”, próbuje utrzymać park maszynowy w wystarczająco dobrej kondycji, aby zapewnić ciągłość produkcji, TPM dąży do osiągnięcia ZERO usterek maszyn, ZERO produkcji wad oraz ZERO
wypadków przy pracy. Pod tym pojęciem doskonałości kryje się zarządzanie zasobami firmy, które, bazując na zdrowym rozsądku, pracy w zespole i praktykach wypracowanych przez firmy, głównie japońskie, umożliwia zwiększanie wydajności pracy, polepszenie jakości produktu i powiększanie rentowności firmy.
Total Productive Maintenance to filozofia zarządzania, włączająca wszystkich pracowników firmy w utrzymanie ciągłości produkcji poprzez zespołowe eliminowanie strat, kierując się wymogami klienta i nastawiając na wypracowanie zysku. TPM łączy w całość usprawniające działania podejmowane przez różne działy przedsiębiorstwa.
Wdrożenie TPM
Wdrożenie TPM często wiąże się z łamaniem stereotypów dotyczących podziału pracy w fabryce na osoby/działy odpowiedzialne za produkowanie, za naprawę maszyn, za wykonywanie przezbrojeń itd. TPM zakłada odpowiedzialność wszystkich za utrzymanie parku maszynowego w idealnym stanie. Kluczowym elementem jest spowodowanie zainteresowania i udziału operatorów w programie usprawnień, bowiem przede wszystkim oni posiadają informacje umożliwiające skuteczne przeciwdziałanie awariom. Bez ich zaangażowania i współpracy nie może zaistnieć efektywne utrzymanie ruchu. Udział operatorów to nie tylko uczynienie ich odpowiedzialnymi za wykonywanie pewnych funkcji przy maszynach, ale również przekazanie im decyzyjności, która będzie wspomagała wykonywanie tych czynności.
W przygotowanie do wdrażania Programu TPM wchodzą działania w trzech głównych obszarach:
- Edukacja wszystkich pracowników przedsiębiorstwa, zaczynając od Top Management, a kończąc na pracownikach liniowych, z celem zmiany świadomości na temat tego, co stanowi efektywny system wytwarzania;
- Stworzenie systemu, który oprze wszelkie działania przy wdrażaniu na pracy w zespołach;
- Rozpoczęcie działań od wprowadzenia 5S, czyli uporządkowania istniejącego stanu poprzez usuniecie rzeczy niepotrzebnych, gruntowne wyczyszczenie firmy i wizualizację zarządzania.
Powiązane wpisy:
- Program CMMS.net
Program CMMS.net to innowacyjna aplikacja dla Służb Utrzymania Ruchu, która umożliwia efektywne zarządzanie procesami utrzymania ruchu w firmie. Dzięki pełnej dokumentacji, planowaniu przeglądów, napraw oraz... - Utrzymanie ruchu maszyn i urządzeń
Sposób utrzymania ruchu określonych maszyn i urządzeń zależy od ich charakterystyki konstrukcyjnej i roli, jaką spełniają w procesie produkcyjnym. Urządzenia skomplikowane, kosztowne i pracujące w... - Program CMMS.net
Program CMMS.net to innowacyjna aplikacja dla Służb Utrzymania Ruchu, która umożliwia efektywne zarządzanie procesami utrzymania ruchu w firmie. Dzięki pełnej dokumentacji, planowaniu przeglądów, napraw oraz... - Służba utrzymania ruchu
TCS.net, opracowany przez firmę SoftwareStudio, to jedno z rozwiązań CMMS, które oferuje kompleksowe funkcjonalności i możliwość dostosowania do indywidualnych potrzeb przedsiębiorstwa....